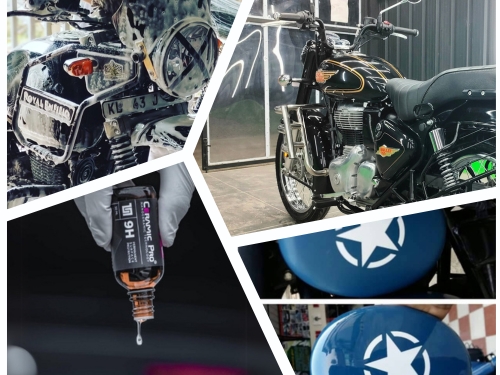
Long story short:Discover the benefits of ceramic coating for your bike. This advanced technology offers exceptional protection against scratches, dirt, and environmental elements, keeping your bike’s paint pristine. It provides strong UV resistance, preventing colour fading and damage from sun exposure. This comprehensive guide will dive into the world of bike ceramic coating.
The motorcycle market in India is not just thriving; it’s a force to be reckoned with. With more and more enthusiasts hitting the roads, the demand for innovative technologies like ceramic coating is not just rising, but it’s a clear sign of a community that’s constantly evolving and embracing new solutions. This revolutionary solution enhances your bike’s aesthetic appeal and provides long-lasting protection against the elements.
In this article, we aim to equip you with the knowledge to make an informed decision about enhancing your riding experience with ceramic coatings for motorcycles in India. This comprehensive guide, which leaves no stone unturned, will ensure you are well-prepared, discussing their advantages, potential downsides, and critical factors to consider before investing, such as cost, application process, and maintenance needs.
Our goal is not just to provide you with the knowledge but also to guide you in making an informed decision about enhancing your riding experience with this cutting-edge technology. We are here to support you and empower you with the right information.
Key Takeaways
- Ceramic coating is like a protective shield for your bike. It’s a liquid polymer applied to the bike’s exterior surfaces, including the paintwork.
- Understanding the concept of ‘hardness’ in ceramic bike coatings is crucial. Hardness refers to the coating’s ability to resist scratches, abrasions, and other physical damage. It is a vital determinant of its performance and durability.
- In the Indian bike market, ceramic coating products typically claim hardness ratings of 9H or 10H.
What is a ceramic coating for bikes?
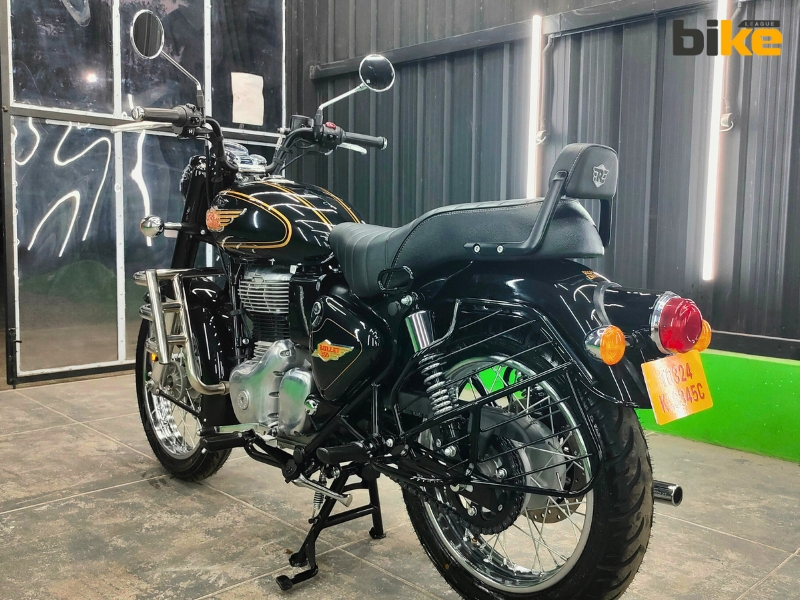
Ceramic coating is like a protective shield for your bike. It’s a liquid polymer applied to the bike’s exterior surfaces, including the paintwork. This coating chemically bonds with the paint, creating a formidable barrier that resists environmental contaminants like UV rays, acid rain, dirt, and grime.
The benefits of bike ceramic coating include long-lasting protection and a glossy finish that keeps your bike looking new for years.
The primary purpose of ceramic coating is to protect the bike’s paintwork from damage, make it easier to clean, and enhance its overall appearance.
What is Hardness in Ceramic Coatings?
In ceramic coatings for bikes, “hardness” refers to the coating’s ability to resist scratches, abrasions, and other physical damage. This property is crucial for several reasons:
- Scratch Resistance: A higher hardness rating indicates better resistance to scratches and abrasions
- Durability: Harder ceramic coatings are more durable, providing long-lasting protection against wear and tear.
- Environmental Protection: Hard ceramic coatings offer superior protection against UV rays, oxidation, and chemical contaminants.
- Ease of Maintenance: A hard ceramic coating creates a smooth surface, making cleaning easier.
- Longevity: Harder coatings generally last longer, reducing the need for frequent reapplications.
There are different measurements of hardness:
- scratch hardness
- indentation hardness
- rebound hardness.
Hardness depends highly on ductility, elastic stiffness, plasticity, strain, strength, toughness, viscoelasticity, and viscosity.
Different Hardness Scale Types
Here, we will focus on Scratch Hardness. These tests determine the hardness of a material to scratches and abrasions. Generally, there are three scales used for determining the hardness of minerals:
1. Mohs Scale
It is based on relative scratch hardness, with talc assigned a value of 1 and diamond assigned a value of 10. Mohs’ scale had two limitations: it needed to be more linear, and most modern abrasives fell between 9 and 10.
2. Ridgway’s Scale
A modification of the Mohs scale by giving garnet a hardness of 10 and diamond a hardness of 15.
3. Wooddell’s Scale
Extension of the Ridgway’s scale by using resistance to abrasion and extrapolating the scale based on seven for quartz and nine for corundum, resulting in a value of 42.4 for South American brown diamond bort.
Pencil Hardness Scale: How does it work
The Mineral Scales (Mohs, Ridgway, and Wooddell) are unsuitable for coatings or films. Therefore, ASTM developed the Pencil Hardness Scale, which uses a graphite pencil rated 1-2H on the Mohs scale for measuring film hardness.
The pencil hardness scale is a detailed measure of graphite hardness. The coatings industry has used this scale for years to assess the hardness of clear and pigmented organic coatings, mainly to evaluate curing, especially when heat is applied.
Grading pencils come in various hardness levels from 10H to 9B and are available at most art or office supply stores. ‘H’ indicates hardness, ‘B’ indicates blackness, and HB stands for hard and black pencils.
The hardness scale ranges from 10H (most challenging) to 9H, 8H, and H, with F in the middle. The softer grades include HB, B, 2B, and 9B (softest). The #2 (HB) is the most commonly used pencil, known for its smoothness and dark marks.
Measurement of Hardness in Ceramic Coatings
The hardness of ceramic coatings is typically measured using the pencil hardness test, widely used in the automotive industry. This test uses pencils of varying hardness to scratch the coating surface and determine its resistance to scratching. The scale ranges from 1H to 9H, with 9H being the hardest.
While the pencil hardness test is the most common method, other scientific approaches, such as the Vickers and Knoop Hardness Tests, are also used. These tests involve diamond indenters to measure the hardness of ceramic materials more precisely. However, they are less commonly referenced in marketing claims.
It’s important to note that the “H” rating in ceramic coatings should not be confused with the Mohs scale of mineral hardness. The Mohs scale ranges from 1 (talc) to 10 (diamond) and is sometimes referenced to provide a relative measure of hardness, b. Still, it’s not directly applicable to ceramic coatings.
Common Hardness Values in the Indian Market
In the Indian bike market, ceramic coating products typically claim hardness ratings of 9H or 10H. These high ratings are often used as selling points to indicate superior protection. Here are some common values and products found in the market:
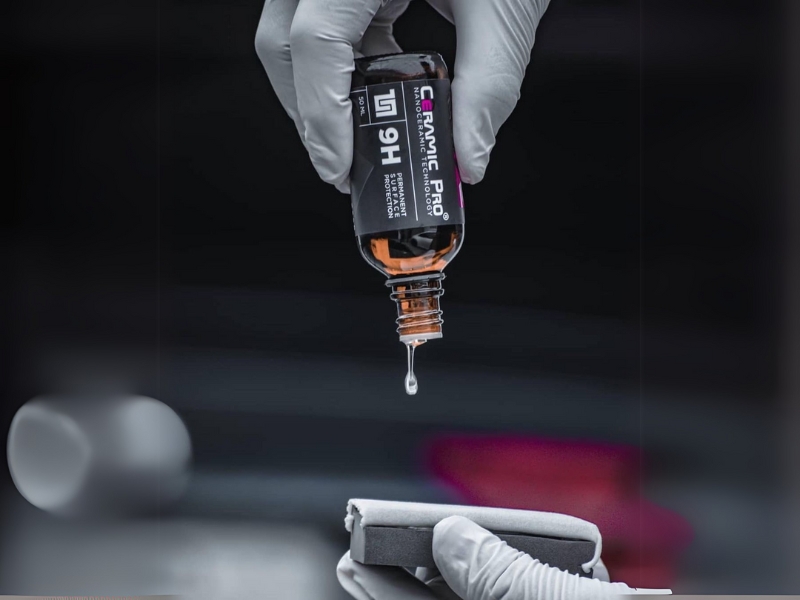
1. 9H hardness:
This is a standard rating for many ceramic coatings available in India. Products with a 9H rating are known for their high scratch resistance and durability. Examples include:
- 3M Ceramic Coating
- Gyeon Quartz coatings
- CarPro ceramic coatings
2. 10H Hardness:
Some products claim an even higher hardness rating of 10H, suggesting enhanced protection. For instance, WaveX 10H Graphene Ceramic Coating is noted for its superior hardness, hydrophobic properties, and long-lasting protection.
3. 9H+ Ratings: Some brands offer products with hardness ratings that exceed 9H but still need to reach 10H. These are often marketed as premium options with enhanced durability.
It’s crucial to approach these hardness claims with a critical eye. Marketing can sometimes exaggerate these values. The actual performance of a ceramic coating depends on various factors beyond hardness, including the quality of the application and the product’s specific formulation. So, it’s essential to be discerning when evaluating these claims.
The Step-by-Step Process of Applying Ceramic Coating to Bikes
While applying ceramic coating might seem straightforward, it’s a meticulous process that demands attention to detail and professional expertise. Here’s a detailed breakdown of the steps in applying ceramic coating to bikes, ensuring every aspect is covered for a thorough application.
1. Initial Cleaning
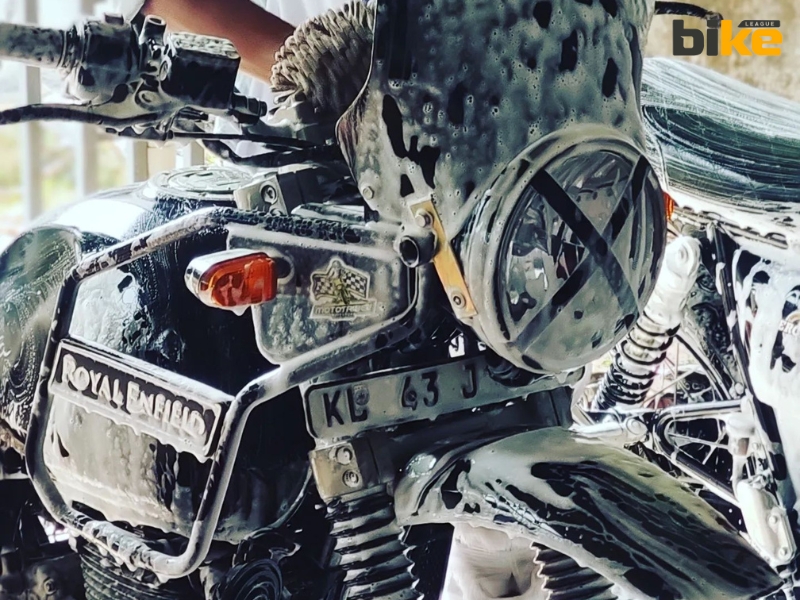
The process begins with a crucial step: thoroughly washing the bike using a high-quality, pH-neutral shampoo. This step is vital as it helps to remove dirt, grease, and other contaminants from the surface, providing a clean canvas for the coating.
2. Rinsing
After allowing the shampoo to dwell for a few minutes, the bike is thoroughly rinsed with a hose or pressure washer. This step ensures that all residues are entirely washed away, leaving a clean surface ready for the ceramic coating. Professionals pay special attention to hard-to-reach areas to ensure no soap residue remains.
3. Surface Preparation
This is the most critical step in the entire process. Professionals inspect the bike’s surfaces for any remaining contaminants. They repeat the cleaning process if necessary until the surfaces are spotless and dry.
For a more detailed preparation, many professionals use a clay bar to remove any embedded contaminants. They spray a lubricant like a quick detailer over a bike section and glide the clay across the surface using straight back-and-forth motions.
4. Paint Correction
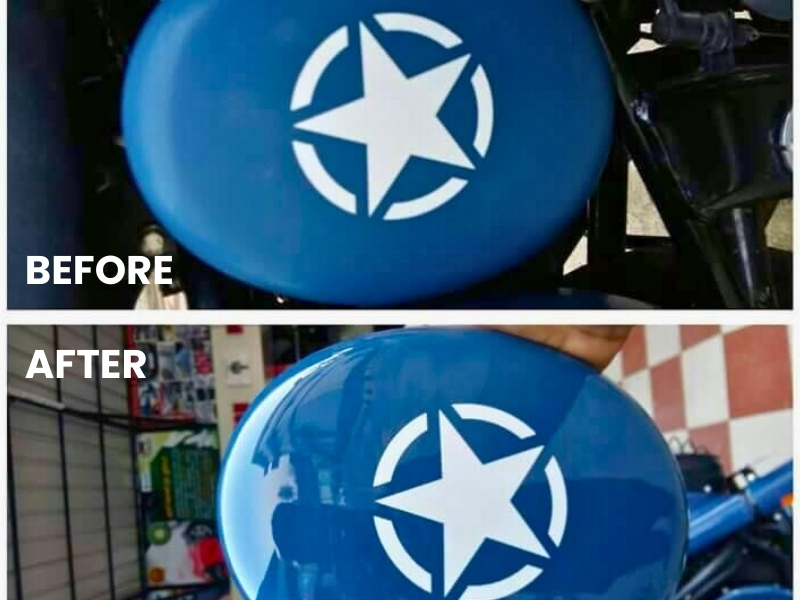
Before applying the ceramic coating, professionals often perform paint correction. This involves using a Dual Action (DA) polisher to remove any imperfections in the paint, such as swirls or scratches, to ensure a smooth surface for the coating. This step is crucial for achieving a flawless finish and maximising the benefits of the ceramic coating.
5. Application of Ceramic Coating
With the surface properly prepared, the actual application of the ceramic coating begins. Professionals follow the instructions provided with the specific ceramic coating product.
Typically, this involves coating in small sections to ensure an even and thin layer. They use a clean applicator pad or cloth, applying the coating in a crosshatch pattern to ensure complete coverage.
6. Buffing and Curing
After applying the ceramic coating, it can cure according to the manufacturer’s recommendations. This step is crucial for the coating to bond properly with the bike’s surface. Once cured, professionals buff the surface with a clean microfiber cloth, revealing a glossy and protected finish.
The Importance of Professional Application of Ceramic Coating
While DIY ceramic coating kits are available, achieving optimal results requires a professional application. Here’s why entrusting your bike to a professional for ceramic coating is crucial:
1. Expertise and Experience
Professional detailers have the expertise to apply ceramic coatings correctly, including surface preparation, application, and proper curing.
2. Superior Surface Preparation
Proper surface preparation is critical to the success of a ceramic coating. Professionals conduct thorough paint decontamination and correction beforehand, as sealing imperfections can make them more visible.
3. Access to High-Quality Products
Professionals use high-quality ceramic coatings that offer superior protection and longevity compared to consumer-grade options.
4. Proper Application Techniques
Applying ceramic coating requires precision and proper techniques to ensure an even layer. Professionals are trained to do this in controlled environments to minimise contamination risks and use specialised tools for an even application, essential for optimal protective and aesthetic benefits.
5. Controlled Curing Process
The curing process is crucial for ceramic coating applications. Professionals know the specific curing requirements, like avoiding water exposure for a set time. They have the facilities to maintain optimal conditions during this period, which can be hard to achieve at home.
6. Long-Term Benefits and Warranty
Professional applications typically include a warranty, ensuring the coating performs as expected. It covers issues like peeling or fading that may not be included in DIY applications. The long-term benefits of enhanced durability and protection often justify the initial cost.
7. Avoiding Common Mistakes
DIY applications often lead to mistakes like uneven product application, insufficient curing time, or inadequate surface preparation. These errors can result in poor outcomes or damage the bike’s paint.
Considerations for Ceramic Coating for Bikes in India
When considering ceramic coating for your bike in India, there are several factors to keep in mind:
- Climate and Environmental Conditions
- Cost Considerations
- Maintenance and Aftercare
India’s varied climate, intense heat and heavy monsoons pose unique bike maintenance challenges. Ceramic coatings offer UV protection against fading and oxidation. At the same time, their hydrophobic properties repel water and dirt, easing upkeep during the rainy season.
Ceramic coating costs depend on bike size, brand, and coating quality in India. Although it involves a significant initial investment, the long-term benefits and maintenance savings are worth it. Although professional applications may be pricier than DIY options, they often provide better quality and durability, making them more cost-effective in the long run.
Regular maintenance is crucial for keeping your bike in top condition, even with a ceramic coating. This includes periodic washing and avoiding abrasive cleaning methods. Some professional services provide warranties and support for ongoing care.
Benefits of bike Ceramic Coating
- Superior Protection Against Environmental Contaminants
- UV Ray Protection
- Hydrophobic Properties
- Enhanced Appearance
- Long-lasting Protection
- Resistance to Minor Scratches
- Ease of Maintenance
The benefits of bike ceramic coating include strong barriers against dirt, acid rain, bird droppings, and tree sap, effectively safeguarding your bike’s paintwork over time.
Other benefits of bike ceramic coating include its ability to protect against UV damage. In India’s intense sunlight, ceramic coatings prevent fading, helping maintain your bike’s original colour for longer.
The hydrophobic nature allows water and liquids to bead up and roll off, making cleaning easier and reducing water spots.
Ceramic coating provides a glossy finish that deepens colour and vibrancy, keeping your bike looking newer for longer.
Unlike traditional waxes, bike ceramic coating offers several years of durable protection, minimising the need for frequent detailing.
Though not scratch-proof, ceramic coatings can help resist minor scratches and preserve your bike’s appearance. This is one of the significant benefits of bike ceramic coating.
Other vital benefits of bike ceramic coating include the smooth ceramic surface, which makes dirt more challenging to adhere to, simplifies the cleaning process, and makes your bike shiny.
Cons and Limitations of Ceramic Coating
- High Initial Cost
- Professional Application Required
- Not Completely Scratch-Proof
- Ongoing Maintenance and Care
- Potential for Misapplication
- Limited Durability
Ceramic coating services for bikes in India can cost between ₹2,500 and ₹15,000, depending on factors like the coating brand and bike size.
Achieving the best results typically necessitates a professional application due to the complex preparation and technique involved.
While ceramic coatings enhance protection, they don’t make bikes entirely scratch-proof and can’t fully resist severe abrasions.
Regular maintenance, including cleaning and possible reapplication, is needed to keep the coating effective.
Improper application can lead to uneven surfaces, highlighting the need for professional services to avoid damage.
Though more durable than waxes, ceramic coatings are not permanent and may require reapplication over time, especially in harsh conditions.
Popular Ceramic Coating Brands in India
Several brands have gained popularity in the Indian market for their ceramic coating products:
- Labocosmetica
- Opti-Coat
- 3M Ceramic Coating
- WaveX Auto Care
- Gyeon Quartz
- CarPro
- Secret Surface Ceramic Coating
- IGL coatings
- Super Ceramic Coating
- DTK Kerala
- Ceramic Pro
These companies offer a range of products and services tailored to different needs and budgets, ensuring bike owners can find a solution that fits their requirements.
FAQ about ceramic coating for bikes in India
1. How long does ceramic coating last on a bike in India?
The longevity of ceramic coatings varies widely, ranging from 6 months to several years, based on product quality and maintenance. With proper care, high-quality coatings can last 2-5 years in Indian conditions.
2. What is the cost of ceramic coating for bikes in India?
The cost of ceramic coating for bikes in India can range from ₹2,500 to ₹15,000 or more, depending on factors such as the brand of coating, size of the bike, and the service provider.
3. Is ceramic coating worth the investment for bikes in India, especially for those under 2 lakh INR?
The value of ceramic coating varies based on the bike’s worth and the owner’s priorities. It may not be cost-effective for bikes under 2 lakh INR. Still, it can be beneficial for those seeking aesthetics and long-term protection.
4. How does ceramic coating compare to traditional waxing or paint protection film (PPF)?
Ceramic coating provides longer-lasting protection and a more durable finish than conventional waxing. Still, it offers less scratch protection than PPF. It is easier to maintain and enhance aesthetics than PPF.
5. Can I apply a ceramic coating or hire a professional?
Ceramic coatings should be professionally applied for the best results. Experts have the skills, tools, and controlled conditions needed for proper preparation and application, ensuring the coating’s effectiveness and durability.
6. How should I maintain my bike after applying ceramic coating?
Maintenance of a ceramic-coated bike involves:
- Regular washing with pH-neutral shampoos.
- Avoiding abrasive cleaning methods.
- Periodic reapplication of a ceramic boost spray.
It’s essential to follow the manufacturer’s guidelines for specific care instructions.
7. Will ceramic coating protect my bike from scratches and UV damage in India’s climate?
Ceramic coating provides excellent protection for bikes from UV rays, helping to prevent paint fading and oxidation. This is particularly beneficial in India’s sunny climate. While it offers some resistance to minor scratches, it’s not entirely scratch-proof.
8. How does ceramic coating affect matte or custom paint finishes?
Ceramic coating can alter the appearance of matte finishes, potentially adding a glossy effect. For custom or matte paint jobs, it’s crucial to use specialised ceramic coatings designed for these finishes or consult a professional to maintain the desired look.
Here are some related articles from our team
- A comprehensive guide to choosing the right bike coating
- Bike fitness certificate guide – All you need to know
- What all basic motorcycle accessories should a rider have
- Motorcycle RC book in India: Exploring Book vs Digital
- Medical Certificate for bike riders in India: Essential Guide
Conclusion
Ceramic coating for bikes in India offers excellent protection against environmental factors. It enhances appearance, making it popular among bike enthusiasts. While bike ceramic coating provides benefits like ease of maintenance and long-lasting results, the high initial cost, need for professional application and ongoing maintenance must be considered.
As the ceramic coating market evolves with new technologies, bike owners should carefully weigh the pros and cons based on their specific needs and budget. For some, regular waxing may be a more suitable option. However, for those willing to invest, ceramic coating can deliver exceptional protection and aesthetic appeal for years on India’s roads.
If you have any questions or need more information, email us at bikeleague2017@gmail.com or leave a comment below. We’re always here and happy to help!. Similarly, don’t forget to check out Bikeleague India on our social media platforms to stay connected!.